The Maison des Métiers d’Art
Frank Sans C had the honour and the privilege of pushing open the doors of the Maison des Métiers d’Art Cartier. The channel was given an exclusive visit to this place known only to the initiated. Artisans, who shall remain faceless, revealed the secrets of the craftsmen’s ancestral techniques. Patience and savoir-faire are key. Where tradition and creativity come together, the extraordinary has no limits.
Frank Sans C ventured into the ateliers of the Maison des Métiers d’Art Cartier, in La Chaux-de-Fonds, Switzerland. Was he able to unlock some of the mysteries that shroud the making of the iconic pieces from the famous French maison? One can only dream… Although, he was given the key to a few of these techniques, some of them very old, that are still captivating the world.
The Métiers d’Art, dedicated to jewellery
The Cartier Crash and its champlevé enamelling
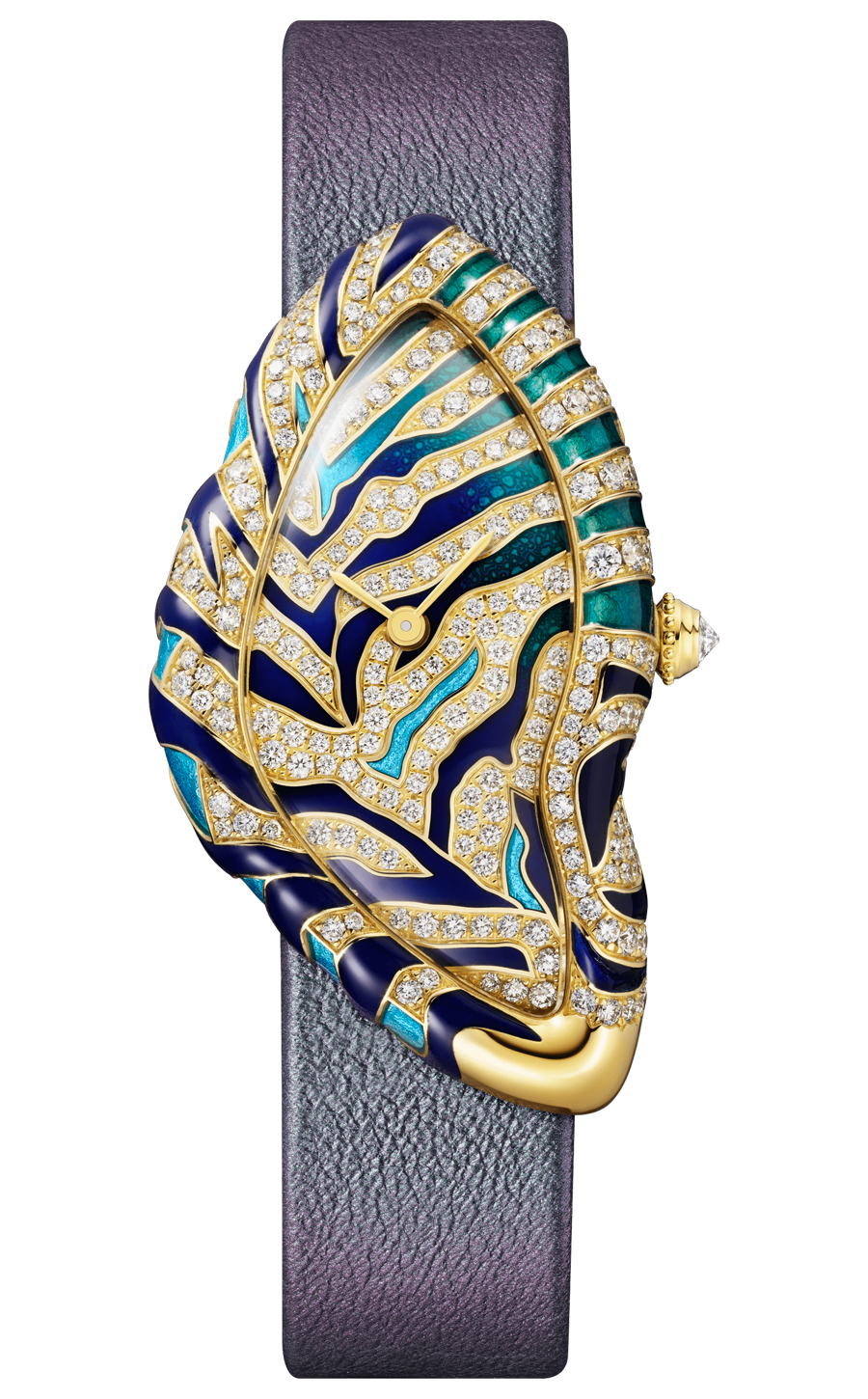
This atypical and iconic piece, created in 1967 in the vibrant and creative Swinging London era, has a unique history. One might think it came straight out of a Salvador Dali painting, but the story is quite different. The watch takes its name, and more importantly, its design, from a person at Cartier, who had an unfortunate car accident. His watch was crushed upon impact – the Crash was born. The watch is often issued in limited runs. This year, its beauty was captured by the skilled hands of jewellers.
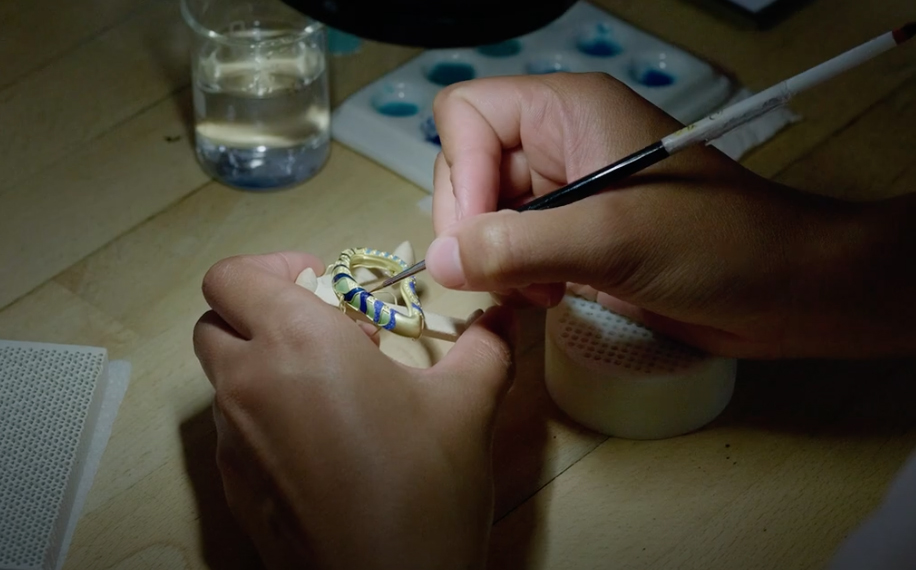
Tigers, crocodiles, water and seashells, the intriguing patterns stimulate the imagination. Diamonds are used in many enamelling techniques. The stripes on the bezel are made of enamel called “champlevé”. French for “raised field”, a lovely term that describes this engraving process. The material – in this case, gold – is finely hollowed out and then filled with enamel.
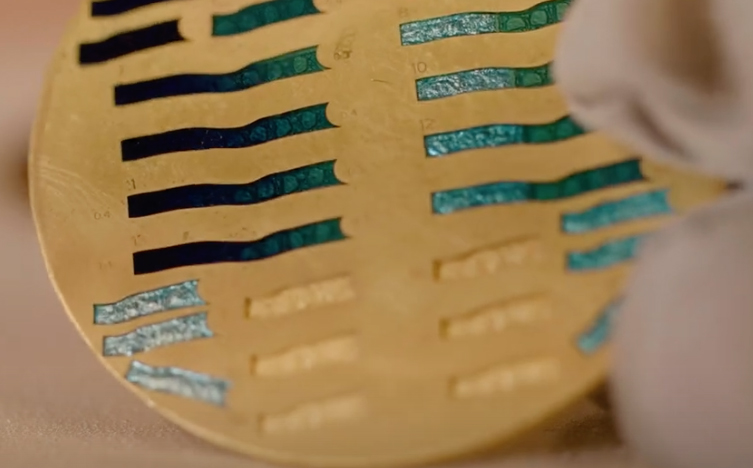
The enamel worker obtains a gradient from blue, to turquoise, to green, from cobalt oxide (blue) and copper oxide (green). The materials then go through ten firing cycles, between 750 and 750 degrees Celsius, to achieve these almost translucent colours. Total mastery.
Limited to 50 pieces
The Coussin de Cartier and its flexible cushion case
Frank Sans C also unveils the trade secrets of the making of the Coussin de Cartier. This model was nominated for the La Montre de l’Année 2022 awards, in its category. State-of-the-art modern techniques at the service of art.
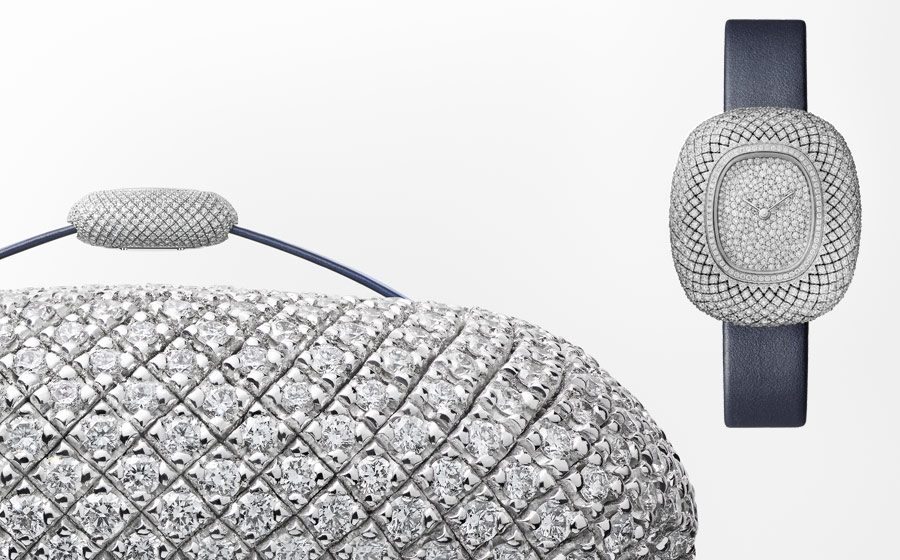
Age-old techniques and the art of composition
Reviving processes and renderings from the past to create tools and techniques that can be applied to the latest innovations and to artisan extravagances. Such is the mission of the Maison des Métiers d’Art.
Gold granulation and marquetry: the Montre Ronde Louis Cartier Zèbre et Girafe
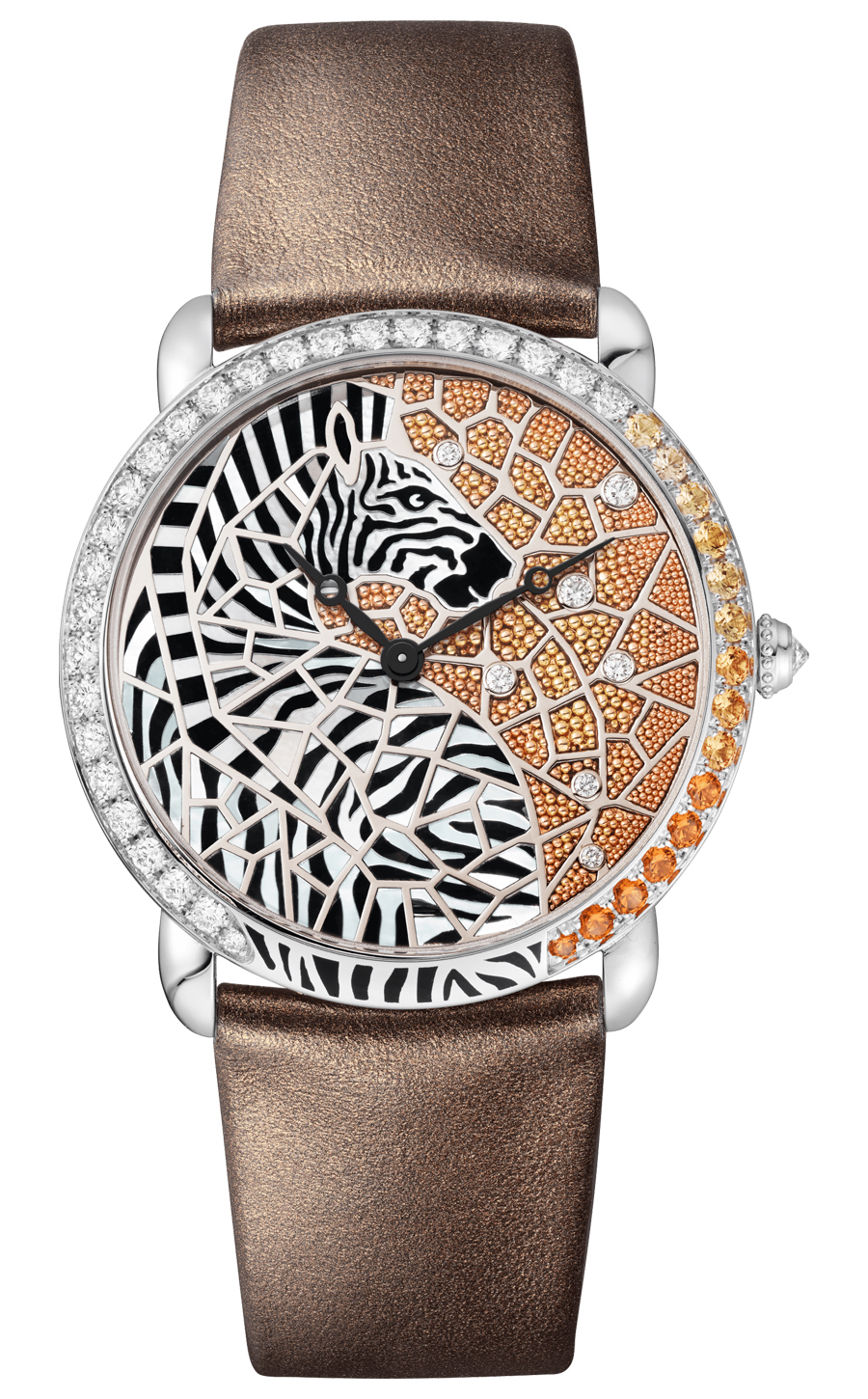
The panther, Cartier’s signature animal since 1914, is a fixture of the maison’s collections. But the feline shares the stage with a whole bestiary, rich in powerful and majestic beasts. Take for example the Montre Ronde Louis Cartier, uniting a zebra’s profile, on one side, with giraffe spots, on the other. Marquetry was used to craft the zebra stripes, in alternating onyx and mother-of-pearl.
This very special and meticulous technique makes use of various materials. In his video, Frank Sans C even mentions woodwork, using paper-thin wood. To craft the animal’s head and capture all of its nuances, shading is required. This is a complex process: The small strips of wood are plunged into Fontainebleau sand (an age-old material), and slightly heated so that they start burning. To achieve the required shades and contrasts, the strips are kept in the sand for varying lengths of time.
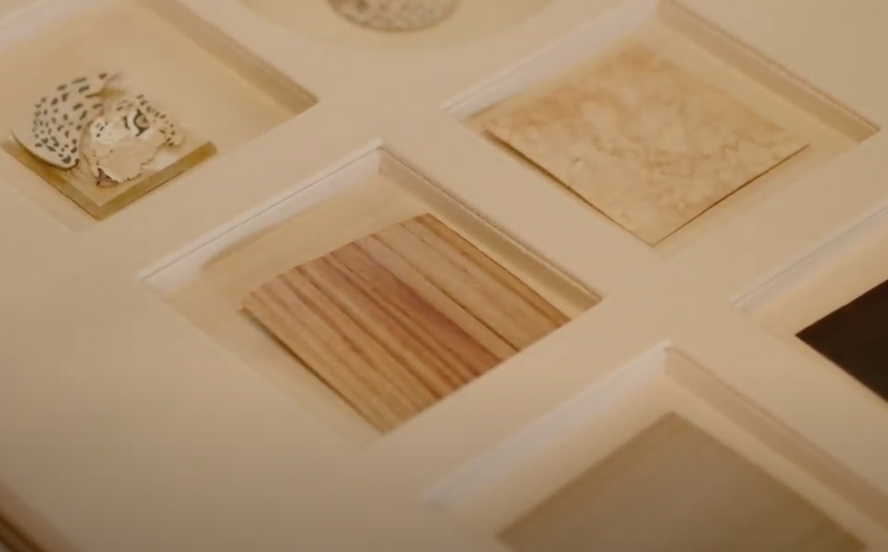
Then comes the tricky part. The artisan selects the perfect grain to be cut out. A micro saw was specially made to carry out this painstaking work.
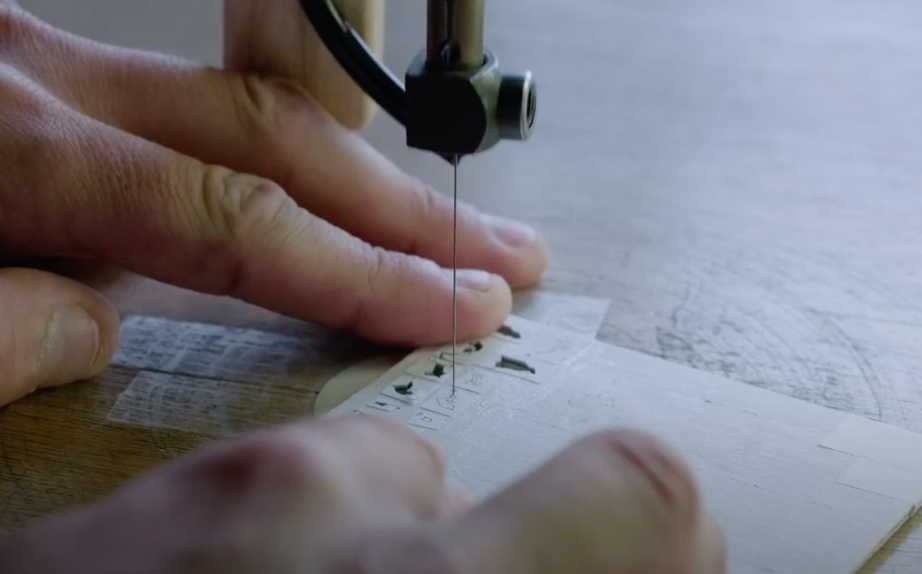
Let’s come back to the Montre Ronde Louis Cartier. After marquetry, then comes gold granulation. This ancient technique, invented by the Etruscans, replicates the giraffe’s spots. The result is highly realistic and is achieved from finely-cut gold threads. When heated, the threads shrink into tiny gold beads. On this project, the artisans used a rose gold and yellow gold gradient for the first time.
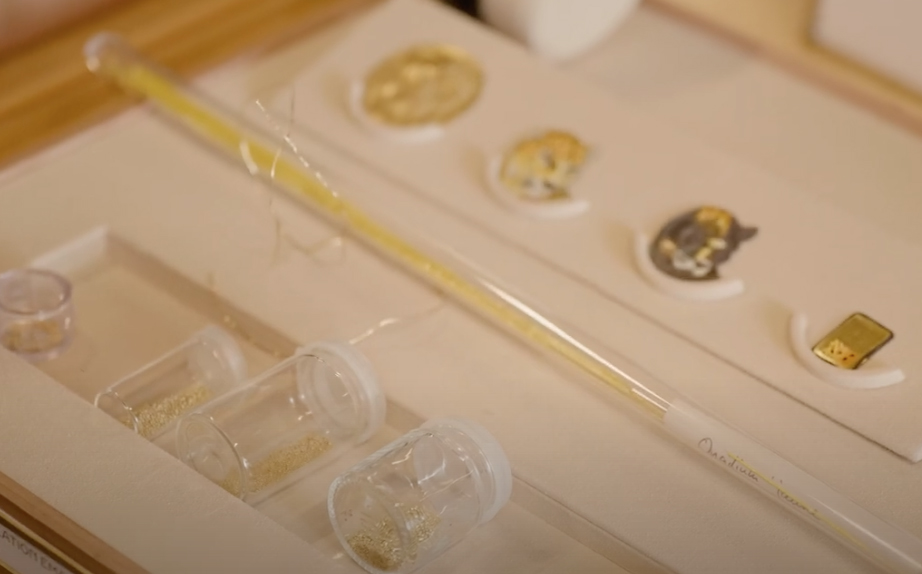
The beads are applied one by one and are of varying sizes to provide contrast to the design. 95 hours of work and seven artistic professions were required to create this limited edition of 30 pieces.
The geometric latticework of the Montre Ronde Louis Cartier Éclats de Panthère Marqueterie
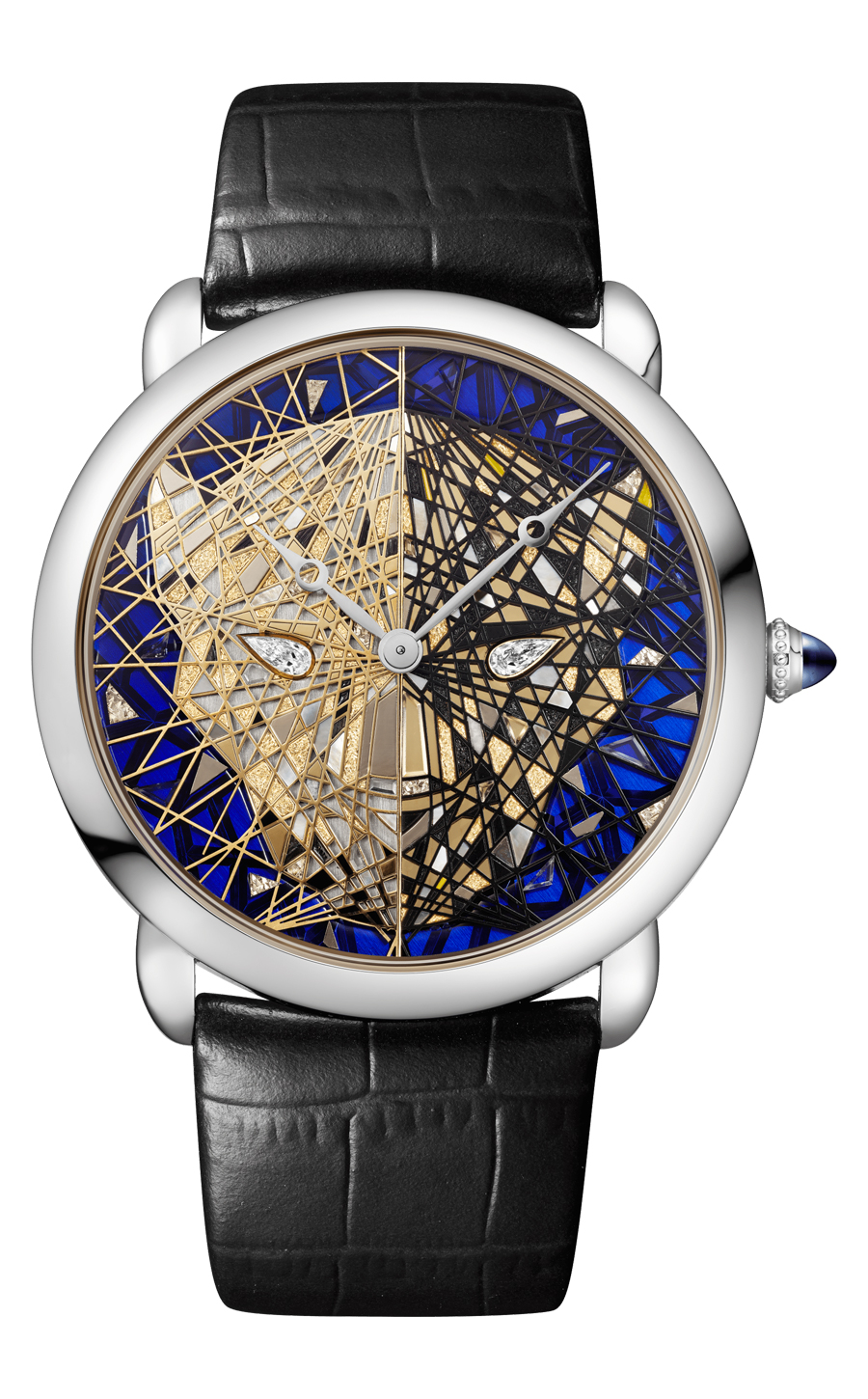
44 hours of marquetry work for this watch limited to 30 pieces. In this latest interpretation, the signature panther takes on a modern and masculine face. In order to achieve this geometric finish, a thin gold lattice is made from 124 separate elements: 16 strands of straw, 8 wood components, 2 yellow gold elements, 34 grey gold elements, 16 fragments of sapphire crystal and 48 fragments of mother-of-pearl. Like futuristic stained glass, the panther’s piercing gaze is mesmerising. A true work of art.
Gem-setting, goldsmithery, grisaille enamelling, mysterious watches, filigrees and even millinery… At Cartier, the possibilities are endless. These expert practices have now been mastered by a new generation of artisans. They have been trained by specialists, guardians of the techniques of yesteryear.
To read also: